Introduction
A DIY Roof Rack was one of the first projects I attempted for my camper conversion in 2018. With limited aftermarket roof rack options for the 2nd generation Transit Connect at the time, I decided to take a risk and figure a solution myself.
PROJECT GOALS:
- End up with a removable/non-permanent, low-profile rack assembly
- Be able to mount at least 200W of rigid solar panels
- Keep the solar panels hidden as much as possible from observers at ground level
- Have the roof rack structure partially conceal/draw attention away from the Maxxair fan installation
After nearly 3 years use, this article will serve both as an assessment of what went right and what didn’t, and a how-to guide featuring how I would redo the project today. There will likely be an update later this summer to rework the rack and make cosmetic improvements
Main Problem
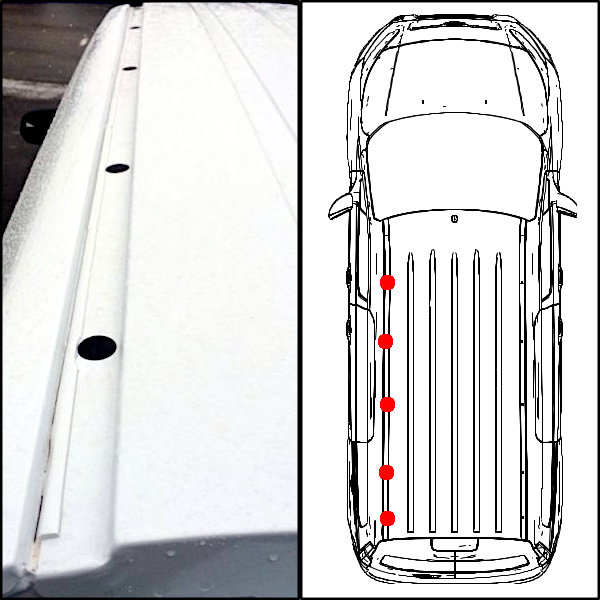
Throw a straight board length-wise across the stock roof rail holes and you can’t miss it. None of the surfaces at each location are flat to each other. Worse, they each slope outward AND either forward or aft, simultaneously, to create a complex contoured surface at each potential roof rack support location.
Early on I knew I wanted to use a length of aluminum angle along each rail to both support and hide the body of the solar panels. In order to do this, I decided to create flat surfaces for the rack supports. These surfaces also needed to seal against water intrusion.
SOLUTION: Liquid Urethane
Materials
Notable Tools
- (4X) Socket Head Cap Screws: 1/4-20 x *4.0″
- (4X) Locknut: 1/4-20
- (4X) Spherical Washer: 1/4-20
- (4X) Oversized Washer: .875 OD for 1/4 ID
- Pack of Neoprene Fender Washers: 1/4 ID
- Smooth-On Clear Flex 95 1 LB or less Part A
- Smooth-On Clear Flex 95 1.5 LB or less Part B
- Model Clay 1+ lbs
I selected solar panels with dimensions that would work with the roughly 46″ spaced roof rail hole arrays. I chose simple pine 2x4s to create the horizontal bracing of the roof rack and the vertical supports.
Dimensions:
- (4X) 2 x 4 x 47.1″ pine
- (4X) 2 x 4 x < *3″ pine (varies)
Tool(s) to accurately cut 2 x 4s to length.
I wouldn’t have been able to do half the projects I’ve completed without metal punches.
Used to create holes in aluminum angles to join 2 x 4s, holes in the wooden vertical rack support legs, and mounting holes in the solar panels.
- Calipers
- Tape Measure
- (1X) Disposable Pitcher
Urethane Pour Process
POST PROJECT NOTES:
- Oversized PVC tube was used to form fastener thru-hole.
- Tape under the PVC tube extremely important to prevent urethane from leaking into the cabin before curing, do not extend tape to edges or water seal will be ruined.
- Tape backing the clay was an unnecessary precaution.
- Clay should have been added to the red box area so that the urethane pad could be poured taller.
POST PROJECT NOTES:
- To aid in accuracy and control during the pouring process while up on a ladder, I used an orange juice container for the handle and spout features.
- Follow Clear Flex mixing directions, IIRC it flash cured in about 14 minutes.
- If you have a mold you want to make with the left-over urethane, have that ready after the pads are poured.
POST PROJECT NOTES:
- Only 3 points needed to create a plane. After pouring all 10 pads, I used only 4 of them for the roof rack support legs.
- Absolutely do not forget to use a release agent before pouring the urethane. Some paint will lift and it will be a painful and slow removal process otherwise.
- Do not spill or trail urethane. If you do, be ready to wipe clean before it cures.
Assembly
The design of the rack allowed for easy assembly off-vehicle. This way, the entire completed assembly could be lifted up onto the roof rack supports (with help) in one piece. Panels were attached underneath the 2 x 4s with typical solar panel “Z-brackets” and gapped with some simple rectangular plexiglass spacers I cut from material on-hand to achieve the slightly recessed panel upper surfaces.
From this
To this
Hardware Stack
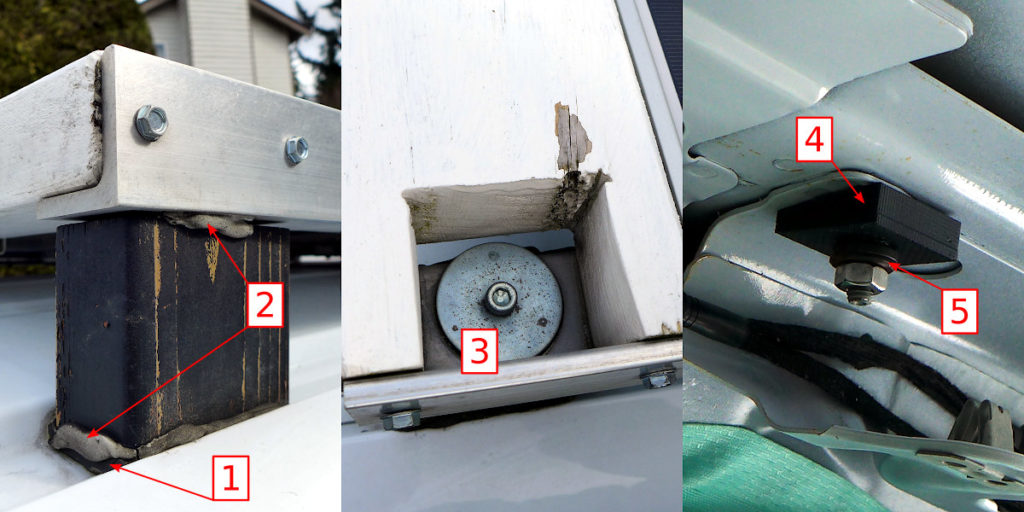
CONNECTION NOTES:
- The polyurethane pad was pretty thin in the upper right corner due to the slope of the van’s roof. This area could’ve benefited from a bit more clay boundary for the pouring operation.
- Butyl Tape Seal sandwiches the both upper and lower vertical rack support surfaces for leak proofing.
- A neoprene washer seals the fender washer (bad) against the aluminum rail.
- The roof skin ceiling happens to be angled as well, but only in one direction thankfully. Here we can use a wedge to bring the fastener mating surfaces close to parallel. I used 3D-printed ABS for this part.
- A spherical washer takes out the rest of the misalignment between the lower surface of the fastener head and the upper surface of the nut to allow for proper tightening of the joint.
What Went Right
After nearly 3 years of use, here’s what went right:
- Aesthetics – the roof rack design hides the panels pretty well from ground level like intended, although I could’ve done a better job on routing the wires.
- Cost – not including the panels, I was into this project for only about $150.
- Sealing – the urethane pads, butyl tape, and neoprene washer have held up well against direct water intrusion.
What Didn't
Three factors contributed to moisture accumulation mostly along the cab ceiling above the headliner. While two of these factors aren’t changing at the moment; living in the PNW, particularly in the winter and spring seasons, and the repeated creation of a large temperature differential by heating the van’s living/cargo area with my Wave 3 Heater, the third factor can. That is, improving the roof rack design to reduce interior condensation accumulation. Below are the highlights, fixes, and general construction improvements I’m planning on implementing later.
TAKE-AWAYS:
The only material that accumulated mold was the OEM sound deadening goop. The Noico sound deadening material had none.
TIP: For a new conversion, I would either remove it (heat gun) or seal in the OEM goop as a first order of business. I chose to seal it up with more Noico.
NOTE: I used too much Noico in this area. Only about 25% coverage is necessary to reduce panel resonance.
That's Mold
Cleaned, Dried, and Sealed
TAKE-AWAYS:
The Thinsulate only accumulated mold around the OEM sound deadening goop. Other areas underneath the roof rack fasteners were wet, but didn’t attract mold. Also, the Thinsulate did not pass any moisture through to the headliner, this was impressive performance as a hydrophobic barrier.
The stock headliner unfortunately doesn’t leave much room between the roof skin for experimentation. Lacking extra Thinsulate, I decided to test EZ-Cool as a replacement radiant barrier.
Crusty
Clean
TAKE-AWAYS:
It wouldn’t have hurt to use stainless steel hardware! The real problem is the wood vertical support leg though. The finish wasn’t properly sealed (Plasti-Dip did not hold up) and the porous wood is likely trapping moisture in the fastener thru-hole and rotting.
TEMPORARY FIX: I cleaned up the length of the fastener with steel wool and coated it with marine grease until I have time for a permanent fix.
PERMANENT FIX: I could cut new lengths of wood for each of the vertical supports and finish all exterior surfaces with much more durable sealant. Instead, I’m planning on 3D-printing each leg in white UV-resistant ASA thermoplastic.
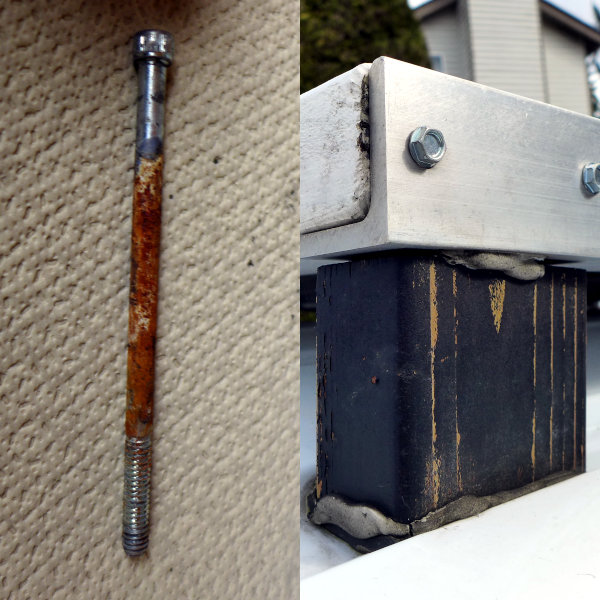
TAKE-AWAYS:
I used what I had on hand which happened to be fender washers. The mating holes on the aluminum angles were drilled oversize to aid in alignment of the roof rack to the stock rail holes. While the fender washers didn’t cause leaks, they were too thin causing deformation from fastener torque (2) and too large to properly seal exposed metal surfaces (1) resulting in thermal bridging and increased condensation in the van interior.
TEMPORARY FIX: I swapped a smaller, thicker washer, taped over the fastener drive hole (3), and applied butyl seal tape (4) to create the thermal break.
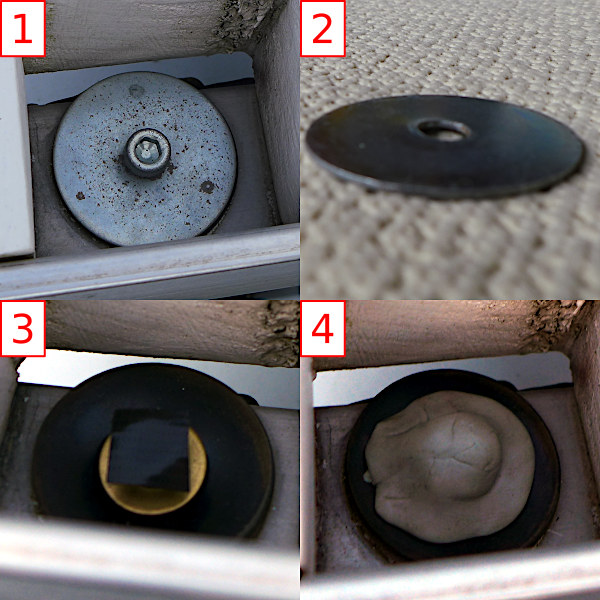
Future Plans
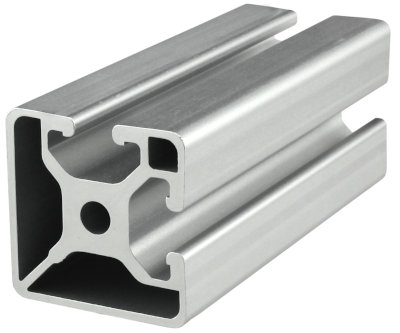
The wood used for the rack supports and horizontal bracing would’ve held up better if I had spent the time filling and sealing all of the cracks and knots. Choice of paint & primer could’ve been better too, perhaps some kind of bed-liner. I could redo each piece, but I think at this point I’d rather switch 40 series 8020 aluminum for the four braces despite the additional expense.
Estimate for Roof Rack Update: Late Summer